Merkmale der Herstellung von Holzbetonblöcken mit eigenen Händen
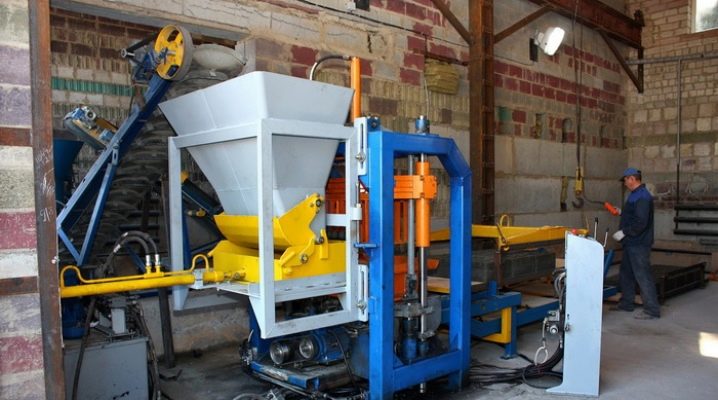
Arbolit wird in vielen Publikationen begeistert beschrieben, Werbetreibende werden nicht müde, ihm verschiedene Vorteile zuzuschreiben. Aber auch ohne Marketing-Gimmicks ist klar, dass dieses Material eine genaue Prüfung verdient. Es ist gut zu wissen, wie man es selbst macht.
Arten und Größen von Blöcken
Arbolite-Platten werden in verschiedene Typen unterteilt:
- großformatige Blöcke (für Mauerkapitelle bestimmt);
- hohle Produkte in verschiedenen Größen;
- Platten zur Verstärkung der Wärmedämmung.
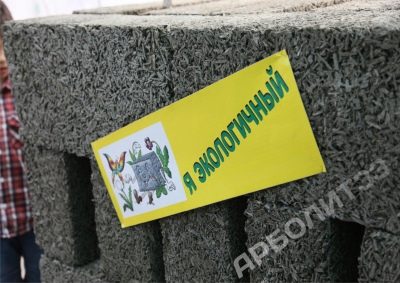
Ebenfalls Holzbeton wird verwendet, um flüssige Mischungen herzustellen, mit dem die umschließenden Strukturen gegossen werden. In der Praxis wird das Wort "Arbolit" jedoch meistens als Mauerwerk mit oder ohne Verkleidung verstanden. Am häufigsten werden Blöcke mit einer Größe von 50x30x20 cm hergestellt, jedoch erweitert sich die Nomenklatur immer mehr und die Hersteller meistern neue Positionen. Die technischen Eigenschaften der hergestellten Blöcke werden nur in Abwesenheit von Verunreinigungen bereitgestellt.
Elemente mit einer Dichte von 500 kg pro 1 cu. m und mehr gelten traditionell als strukturell, weniger dicht - für die Wärmedämmung bestimmt. Sie können dort eingesetzt werden, wo die Last von oben von anderen Bauteilen aufgenommen wird. Normalerweise wird die Dichte erst gemessen, nachdem der Block die überschüssige Feuchtigkeit verloren hat.
Aus Holzgussbeton mit einem spezifischen Gewicht von 300 kg pro 1 cu. m.-Wände können ebenfalls errichtet werden, stehen aber in der Festigkeit Konstruktionen aus schwererem Material in nichts nach.
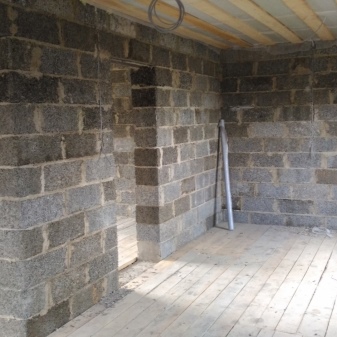
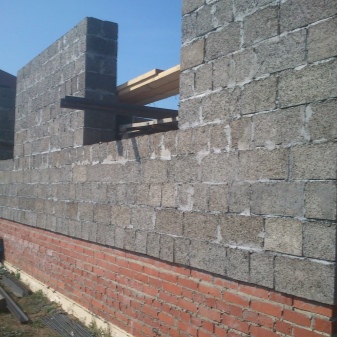
Um Träger zu bauen Wände von einstöckigen Häusern, deren Höhe 3 m nicht überschreitet, müssen Blöcke der mindestens Kategorie B 1.0 verwendet werden... Wenn die Strukturen oben, Produkte der Kategorie 1.5 sind erforderlich und höher. Zweistöckige und dreistöckige Gebäude sollten jedoch aus Holzbeton der Gruppe B 2.0 bzw. B 2.5 gebaut werden.
Nach dem russischen GOST sollten Holzbeton-Umschließungsstrukturen in einer gemäßigten Klimazone eine Dicke von 38 cm haben.
Tatsächlich sind die Wände von Wohngebäuden aus Blöcken von 50x30x20 cm normalerweise in einer Reihe streng flach ausgelegt. Ist eine zusätzliche Wärmedämmung erforderlich, wird ein sogenanntes Warmputzsystem aus Holzbeton hergestellt... Es wird hergestellt, indem Perlit hinzugefügt und eine Schicht von 1,5 bis 2 cm erstellt wird.
Wenn die Räumlichkeiten nicht oder von Zeit zu Zeit beheizt werden, verwenden Sie die Methode des Mauerwerks am Rand. Wärmeabschirmende Holzbetonsteine haben einen Wasseraufnahmekoeffizienten von nicht mehr als 85 %. Bei Strukturelementen liegt der zulässige Wert um 10 % niedriger.
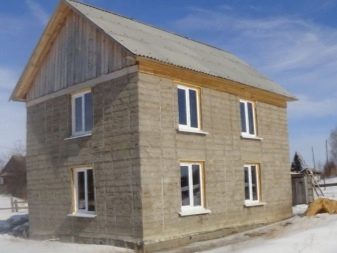
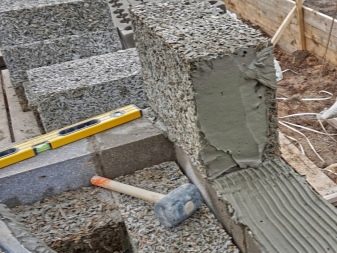
Es ist üblich, Holzbetonsteine nach Brandschutz in drei Kategorien einzuteilen:
- D1 (schwer Feuer zu fangen);
- IN 1 (hochentzündlich);
- D1 (raucharme Elemente).
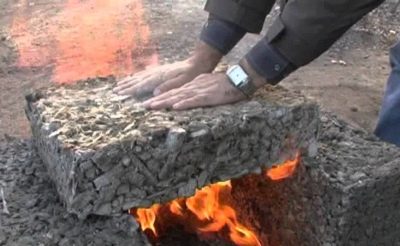
Die Notwendigkeit, Holzbeton zu Hause herzustellen, ist weitgehend darauf zurückzuführen, dass bestehende Hersteller oft minderwertige Waren produzieren. Probleme können hauptsächlich mit unzureichender Festigkeit, schwacher Wärmeübertragungsbeständigkeit oder Verletzung geometrischer Parameter verbunden sein. Blöcke jeglicher Art sollten unbedingt mit Gips abgedeckt werden.... Es schützt zuverlässig vor Wind. Nur „atmungsfähige“ Deckbeschichtungen werden mit Holzbeton kombiniert..
Es gibt 6 Marken von Holzbetonblöcken, die sich durch die Frostbeständigkeit (von M5 bis M50) unterscheiden. Die Zahl nach dem Buchstaben M zeigt an, wie viele Übergangszyklen durch null Grad diese Blöcke übertragen können.
Minimale Frostbeständigkeit bedeutet, dass die Produkte nur für innere Trennwände verwendet werden sollten.
Meistens beträgt ihre Größe 40x20x30 cm Je nach Gerät des Rillen-Kamm-Systems hängen die Fläche des Mauerwerks und die Wärmeleitfähigkeit der Wände ab.
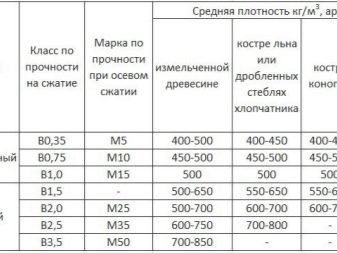
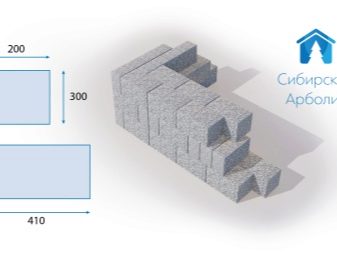
Wenn man über die Abmessungen und Eigenschaften von Holzbetonblöcken nach GOST spricht, kann man nicht umhin zu sagen, dass die maximalen Maßabweichungen streng geregelt sind. So, die Länge aller Rippen darf von den angegebenen Indikatoren um nicht mehr als 0,5 cm . abweichen... Der größte Diagonalunterschied beträgt 1 cm Die Verletzung der Geradheit der Profile jeder Oberfläche sollte nicht mehr als 0,3 cm² betragen... Je höher die Struktur, desto weniger Nähte gibt es bei der Installation und desto geringer ist die Anzahl der Nähte.
In einigen Fällen sind Blöcke mit einer Größe von 60x30x20 cm am bequemsten, sie werden benötigt, wenn die Länge der Wände ein Vielfaches von 60 cm beträgt, wodurch das Zuschneiden von Blöcken entfällt.
Manchmal wird der sogenannte "nördliche Arbolit" gefunden, dessen Länge 41 cm nicht überschreitet.In einigen Reihen stimmt die Breite der Wand beim Bandagieren mit der Länge des Blocks überein, und im anderen Teil ist die Summe der beiden Breiten und der sie trennenden Naht.
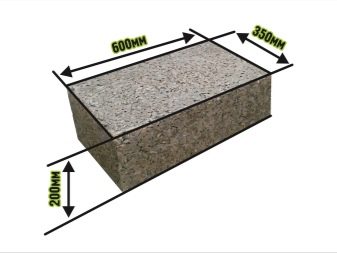
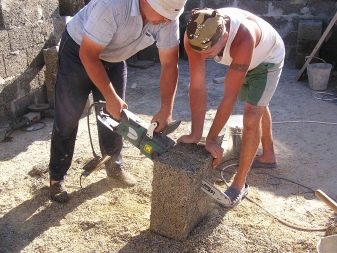
Fast alle Hersteller stellen Prallplatten her. In der Linie jedes Unternehmens beträgt die Größe solcher Produkte 50% der Standardgröße. Gelegentlich finden sich auch Konstruktionen von 50x37x20 cm, mit denen Sie Wände exakt 37 cm errichten können, ohne auf Verbandklötze oder das Anbringen von Paneelen zurückgreifen zu müssen.
In manchen Regionen können ganz unterschiedliche Größen auftreten, dies sollte zusätzlich angegeben werden. Bei Eigenproduktion müssen diese nach eigenem Ermessen ausgewählt werden.
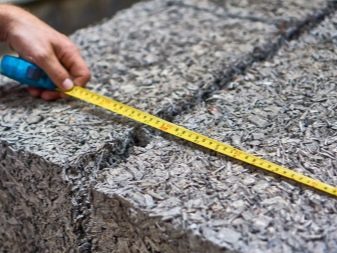
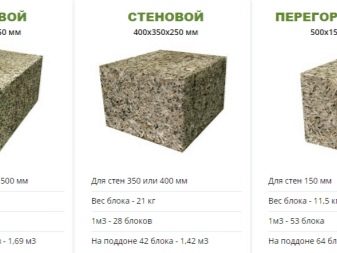
Zusammensetzung und Proportionen der Mischung
Bei der Vorbereitung der Herstellung von Holzbetonplatten müssen die Zusammensetzung der Mischung und das Verhältnis zwischen ihren Teilen sorgfältig ausgewählt werden. Abfälle aus der Holzverarbeitung wirken ausnahmslos als Füllstoff. Da Holzbeton jedoch eine Betonart ist, enthält er Zement.
Dank organischer Komponenten speichert das Material die Wärme perfekt und lässt Fremdgeräusche nicht durch. Wenn jedoch die Grundproportionen verletzt werden, werden diese Eigenschaften verletzt.
Es versteht sich, dass nur einige Arten von Spänen für die Herstellung von Holzbeton verwendet werden können. Dies ist der wesentliche Unterschied zu Sägemehlbeton. Nach der aktuellen GOST sind die Abmessungen und geometrischen Eigenschaften aller Fraktionen des Materials streng geregelt.
Späne werden durch Zerkleinern von nicht marktfähigem Holz hergestellt. Die Länge der Chips variiert zwischen 1,5 und 4 cm, ihre maximale Breite beträgt 1 cm und die Dicke sollte nicht mehr als 0,2 - 0,3 cm betragen.
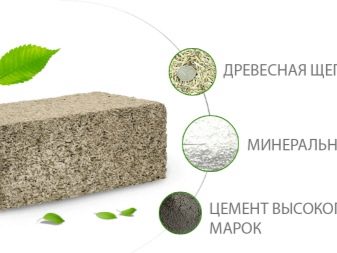
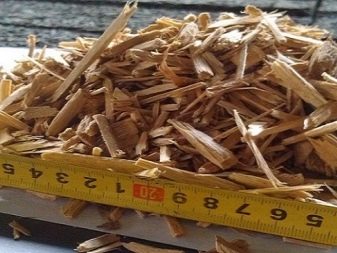
Als Ergebnis spezieller wissenschaftlicher und praktischer Forschung wurde festgestellt, dass die besten Hackschnitzel:
- ähnelt in der Form einer Schneidernadel;
- hat eine Länge von bis zu 2,5 cm;
- hat eine Breite von 0,5 bis 1 und eine Dicke von 0,3 bis 0,5 cm.
Der Grund ist einfach: Holz mit unterschiedlichen Anteilen nimmt Feuchtigkeit unterschiedlich auf. Die Einhaltung der von den Forschern empfohlenen Maße ermöglicht es, den Unterschied auszugleichen.
Neben der Größe müssen die Holzarten sorgfältig ausgewählt werden. Fichte und Buche funktionieren, aber Lärche funktioniert nicht. Sie können Birken- und Espenholz verwenden.
Unabhängig von der gewählten Rasse ist es unbedingt erforderlich, antiseptische Mischungen zu verwenden.
Sie verhindern das Auftreten von Schimmelnester oder die Schädigung von Rohstoffen durch andere pathologische Pilze.
Bei der Herstellung von Holzbeton werden manchmal Rinde und Nadeln verwendet, deren maximaler Anteil jedoch 10 bzw. 5 % beträgt.
Manchmal nehmen sie auch:
- Flachs- und Hanffeuer;
- Reisstroh;
- Baumwollstiele.
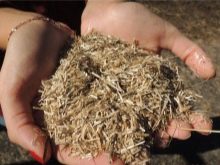
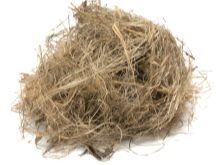
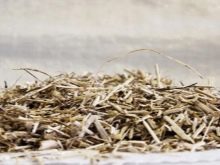
Der größte Die Länge solcher Komponenten beträgt maximal 4 cm und die Breite sollte nicht mehr als 0,2 - 0,5 cm betragen.Es ist verboten, Schleppen zu verwenden und mehr als 5% der Masse zu schleppen gebrauchter Füller. Wenn Flachs verwendet wird, muss es 24-48 Stunden in Kalkmilch eingeweicht werden. Dies ist viel praktischer als 3 oder 4 Monate im Freien. Wenn Sie nicht auf eine solche Verarbeitung zurückgreifen, zerstört der im Flachs enthaltene Zucker den Zement.
Was den Zement selbst betrifft, Portlandzement wird am häufigsten für die Herstellung von Holzbeton verwendet... Er war es, der vor einigen Jahrzehnten für diesen Zweck eingesetzt wurde. Manchmal werden dem Portlandzement Hilfsstoffe zugesetzt, die die Frostbeständigkeit von Bauwerken erhöhen und ihre sonstigen Eigenschaften verbessern. In einigen Fällen kann auch sulfatbeständiger Zement verwendet werden. Es widersteht effektiv den Auswirkungen einer Reihe von aggressiven Substanzen.
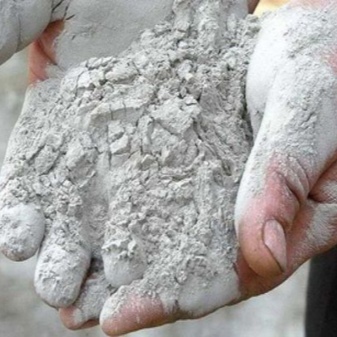
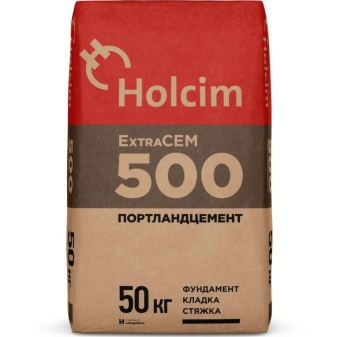
GOST verlangt, dass dem wärmedämmenden Holzbeton nur Zement der Güteklasse M-300 und höher zugesetzt wird. Für Strukturblöcke wird nur Zement einer Kategorie von nicht weniger als M-400 verwendet. Was die Hilfszusätze betrifft, so kann ihr Gewicht 2 bis 4 % des Gesamtgewichts des Zements betragen. Die Anzahl der eingeführten Komponenten wird durch die Marke der Holzbetonblöcke bestimmt. Calciumchlorid und Aluminiumsulfat werden in einem Volumen von nicht mehr als 4% verbraucht.
Das gleiche ist die Grenzmenge einer Mischung von Calciumchlorid mit Natriumsulfat. Es gibt auch einige Kombinationen, bei denen Aluminiumchlorid mit Aluminiumsulfat und Calciumchlorid kombiniert wird. Diese beiden Zusammensetzungen werden in einer Menge von bis zu 2% der Gesamtmasse des verlegten Zements verwendet. In jedem Fall beträgt das Verhältnis zwischen den Hilfsadditiven 1: 1... Damit die adstringierenden Komponenten jedoch effektiv wirken, müssen Sie Wasser verwenden.
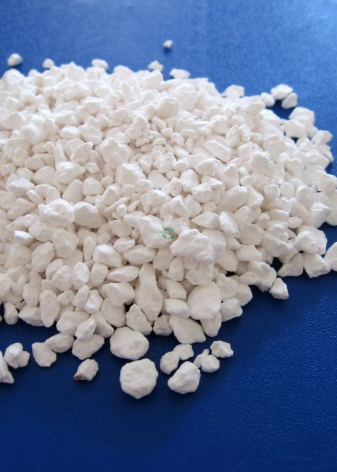
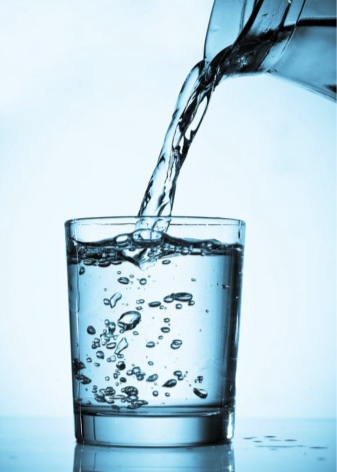
Die GOST schreibt strenge Anforderungen an die Reinheit der verwendeten Flüssigkeit vor. Bei der eigentlichen Herstellung von Holzbeton nehmen sie jedoch oft jedes technisch geeignete Wasser auf. Normales Abbinden von Zement erfordert eine Erwärmung bis zu +15 Grad... Sinkt die Wassertemperatur auf 7-8 Grad Celsius, laufen chemische Reaktionen viel langsamer ab. Das Verhältnis der Komponenten wird so gewählt, dass die erforderliche Festigkeit und Dichte des Holzbetons erreicht wird.
Arbolite-Produkte können mit Stahlgeweben und -stäben verstärkt werden. Hauptsache, sie entsprechen den Industriestandards.
Die Norm verlangt von den Herstellern, die vorbereitete Mischung zweimal pro Schicht oder öfter auf Einhaltung der folgenden Indikatoren zu testen:
- Dichte;
- einfaches Styling;
- Neigung zur Delamination;
- die Anzahl und Größe der Hohlräume, die die Körner trennen.
Die Prüfung erfolgt in einem speziellen Labor. Sie wird für jede Charge der Mischung 7 und 28 Tage nach dem Härten durchgeführt. Die Frostbeständigkeit muss sowohl für dekorative als auch tragende Schichten bestimmt werden.
Um die Wärmeleitfähigkeit herauszufinden, messen sie diese an Proben, die nach einem speziellen Algorithmus ausgewählt werden. Die Bestimmung des Feuchtigkeitsgehalts erfolgt an Proben, die aus fertigen Steinblöcken entnommen wurden.
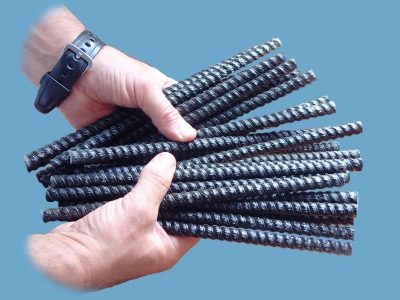
Notwendige Ausrüstung
Nur wenn alle Anforderungen von GOST erfüllt sind, ist es möglich, eine bestimmte Holzbetonmarke in die Produktion aufzunehmen. Um jedoch die strikte Einhaltung der Standards zu gewährleisten und die erforderliche Menge der Mischung freizugeben und dann davon zu blockieren, hilft nur eine spezielle Ausrüstung. Mit industriellen Schleifmaschinen werden Späne in Teile zerlegt. Außerdem gelangt es zusammen mit anderen Komponenten in die Vorrichtung, die die Lösung bewegt.
Sie benötigen außerdem:
- Apparate zum Dosieren und Formen von Holzbetonblöcken;
- Vibrationstisch, der ihnen die notwendigen Eigenschaften verleiht;
- Geräte zum Trocknen von Chips und gekochten Blöcken;
- Bunker, in denen Sand und Zement verlegt werden;
- Leitungen, die Rohstoffe liefern.
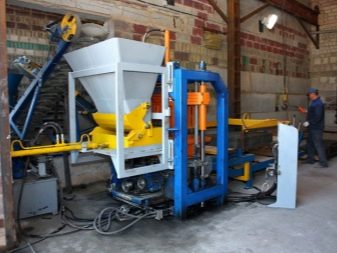
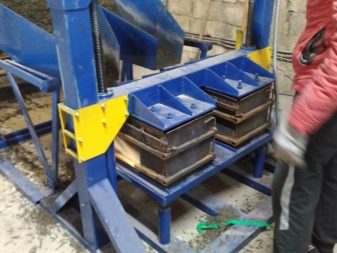
Sie sollten keine selbstgebauten Geräte verwenden, wenn Sie große Mengen Holzbeton herstellen möchten. Sie sind nicht produktiv genug, weil die Rentabilität des Unternehmens sinkt.
Es ist nützlich, die Merkmale der einzelnen Gerätetypen zu berücksichtigen. Zerspanungsgeräte haben eine spezielle Trommel mit "Messern" aus hochwertigem Werkzeugstahl. Darüber hinaus ist die Trommel mit Hämmern ausgestattet, die eine Automatisierung der Rohstoffzufuhr für die anschließende Zerkleinerung ermöglichen.
Damit das Rohmaterial nach innen gelangen kann, ist die Trommel perforiert, sie ist von mehreren umgeben. Eine größere (äußere) Trommel gleicher Form, die das Verstreuen von Schmutz verhindert.Normalerweise wird das Gerät auf Rahmen mit Drehstrom-Elektromotoren montiert. Nach dem Spalten werden die Späne dem Trockner zugeführt. Es ist die Qualität dieses Geräts, die die Perfektion des Endprodukts am stärksten beeinflusst..
Der Trockner ist ebenfalls in Form einer Doppeltrommel hergestellt, sein Durchmesser beträgt ca. 2 m, die äußere Trommel ist perforiert, wodurch die Zufuhr von warmer Luft ermöglicht wird. Die Zuführung erfolgt über ein Asbestrohr oder einen flexiblen feuerfesten Schlauch. Durch das Verdrehen der Innentrommel können sich die Späne rühren und verhindern, dass sich das Rohmaterial entzündet. Eine hochwertige Trocknung kann 90 oder 100 Blöcke in 8 Stunden in den gewünschten Zustand bringen... Der genaue Wert hängt nicht nur von seiner Leistung ab, sondern auch von den Abmessungen der verarbeiteten Strukturen.
Der Rührer ist ein großer zylindrischer Bottich. Alle benötigten Rohstoffe werden von der Seite geladen und die gemischte Zusammensetzung kommt von unten heraus. Typischerweise befinden sich Elektromotoren und deren Getriebe oben auf dem Mörtelmischer. Diese Motoren sind mit Messerbaugruppen ausgestattet. Die Kapazität des Tanks wird durch die Tageskapazität der Leitung bestimmt. In der Miniaturproduktion werden pro Tagschicht nicht mehr als 1000 Designs produziert, während Bottiche mit einem Fassungsvermögen von 5 Kubikmetern verwendet werden. m.
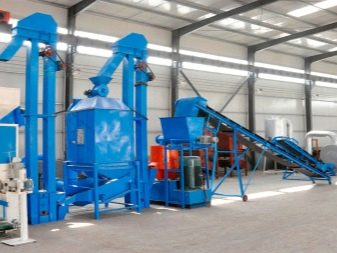
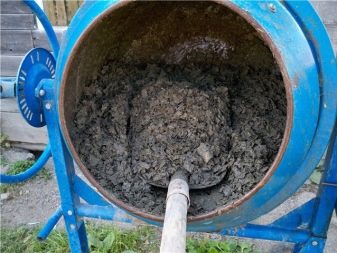
Produktionstechnologie
Um Holzbetonblöcke mit eigenen Händen für ein Privathaus vorzubereiten, müssen Sie 1 Teil Späne und 2 Teile Sägemehl verwenden (obwohl in einigen Fällen ein Verhältnis von 1: 1 bevorzugt wird). In regelmäßigen Abständen wird all dies richtig getrocknet. Sie werden 3 bis 4 Monate im Freien gehalten. Periodisch gehacktes Holz wird mit Kalk behandelt, umgedreht. Normalerweise 1 Kubikmeter. m.-Chips verbrauchen ca. 200 Liter Kalk in einer Konzentration von 15%.
Der nächste Schritt bei der Herstellung von Holzbetonblöcken zu Hause besteht darin, Holzspäne zu mischen mit:
- Portland-Zement;
- gelöschter Kalk;
- Kaliumchlorid;
- flüssiges Glas.
Machen Sie am besten Blöcke von 25x25x50 cm zu Hause.... Diese Dimensionen sind sowohl für den Wohnungs- als auch für den Industriebau optimal.
Die Verdichtung des Mörtels erfordert den Einsatz von Vibrationspressen oder Handstampfern. Wenn nicht viele Teile benötigt werden, kann eine Miniaturmaschine verwendet werden. Spezielle Formen helfen, die genaue Größe des fertigen Produkts einzustellen.
Schalung von Brammen
Sie können einen monolithischen Holzbeton herstellen, indem Sie die vorbereitete Mischung manuell in diese Form gießen. Wenn flüssiges Glas hinzugefügt wird, wird das fertige Produkt härter, aber gleichzeitig nimmt seine Zerbrechlichkeit zu. Es ist ratsam, die Komponenten nacheinander und nicht alle zusammen zu kneten. Dann besteht weniger Klumpengefahr. Eine leichte Konstruktion zu erhalten ist sehr einfach - Sie müssen nur einen Holzblock in die Form legen.
Das Werkstück muss mindestens 24 Stunden in Form gehalten werden... Dann beginnt die Lufttrocknung unter einem Baldachin. Die Trocknungszeit wird durch die Lufttemperatur bestimmt, und wenn sie sehr niedrig ist, dauert sie manchmal 14 Tage. Und die anschließende Flüssigkeitszufuhr bei 15 Grad dauert 10 Tage. In diesem Stadium wird der Block unter dem Film gehalten.
Damit die Holzbetonplatte länger hält, sollte sie nicht auf eine negative Temperatur abgekühlt werden. Holzbeton trocknet an einem heißen Sommertag fast unweigerlich aus. Dies kann jedoch durch regelmäßiges Besprühen mit Wasser vermieden werden. Die sicherste Methode ist die Verarbeitung unter vollständig kontrollierten Bedingungen in einer Trockenkammer. Gewünschte Parameter - Aufheizen auf 40 Grad bei einer Luftfeuchtigkeit von 50 bis 60%.
Informationen zum Herstellen von Holzbetonblöcken mit eigenen Händen finden Sie im nächsten Video.
Der Kommentar wurde erfolgreich gesendet.