Anlagen zur Herstellung von Holzbetonsteinen
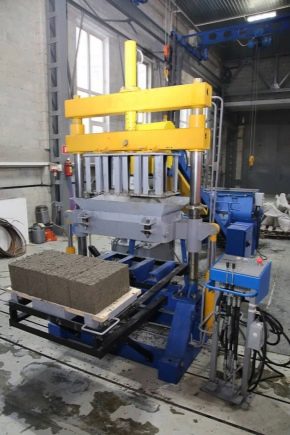
Mittels spezieller Anlagen wird die Herstellung von Arboblöcken realisiert, die über hervorragende Wärmedämmeigenschaften und ausreichende Festigkeitseigenschaften verfügen. Dafür sorgt eine spezielle Fertigungstechnologie. Zur Bildung von Baustoffen werden Zement und Holzspäne verwendet, die einer speziellen Verarbeitung unterzogen werden.
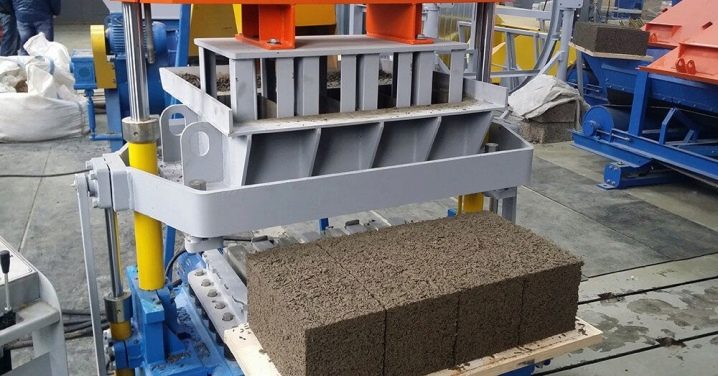
Was ist Holzbeton?
Arbolit (Holzblock, Holzbeton) ist ein fortschrittlicher Baustoff, der durch Mischen und Pressen von Holzspänen (Spänen) und Zementmörtel gewonnen wird. Laut Experten kann es problemlos mit Ziegeln konkurrieren. Gleichzeitig ist Holzbeton jedoch viel billiger.
Hackschnitzel sind die Basis von Holzblöcken. An Parameter und Volumen werden strenge Anforderungen gestellt - diese beiden Eigenschaften haben großen Einfluss auf die Qualität des Endprodukts und seiner Marke. Darüber hinaus gibt es Holzbetonproduktionsanlagen, die Baumwollstroh, Reisstroh oder Baumrinde verwenden.
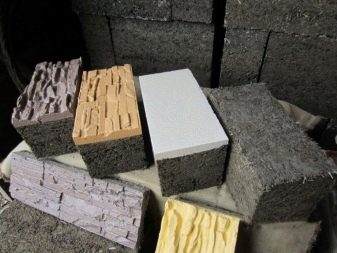
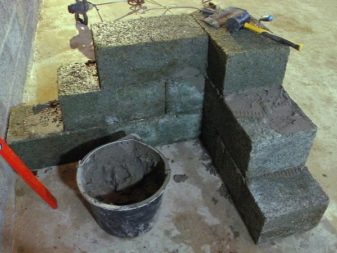
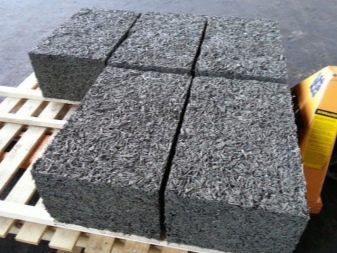
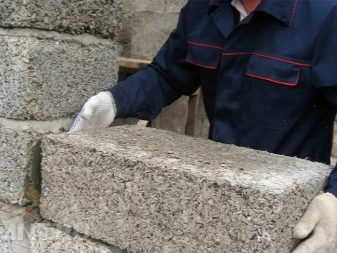
Bindemittel ist Portlandzement der Güteklasse M300 oder höher. Seine Vielfalt hat Einfluss auf die Stabilität des Endprodukts und damit auf seine Kennzeichnung.
Um die Effizienz der Synthese der Inhaltsstoffe der Lösung zu erhöhen, werden spezielle Zusatzstoffe beigemischt, die eine schnelle Aushärtung gewährleisten usw. Die meisten von ihnen sind eine wässrige Lösung von Natrium- oder Kaliumsilikaten (Wasserglas), Aluminiumchlorid (Aluminiumchlorid).
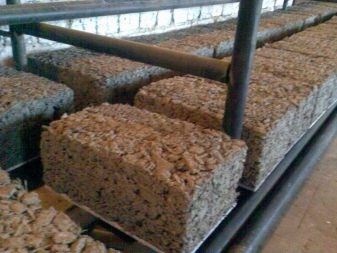
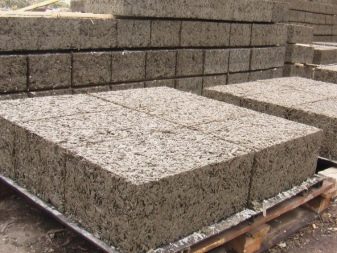
Notwendige Ausrüstung für die Produktion
Um zu Hause Holzbetonblöcke herzustellen, benötigen Sie drei Arten von Geräten: ein Aggregat zum Hacken von Holzspänen, einen Betonmischer oder Betonmischer und eine Maschine zum Formen von Holzblöcken. Aber das Hauptmaterial - Chips, können von Drittherstellern bezogen werden, in diesem Fall wird der technologische Prozess viel einfacher.
Für die Herstellung von Arboblöcken gibt es auf dem Markt ein recht umfangreiches Angebot an Geräten – von kleinen Einheiten speziell für die Kleinserienfertigung bis hin zu vollwertigen Produktionslinien mit mehreren Gerätetypen.
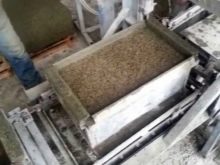
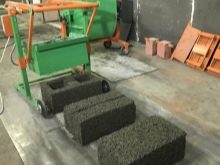
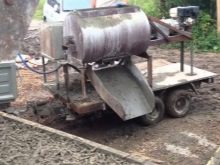
Späneschneider
Eine Vorrichtung zur Herstellung von Holzspänen wird als Hackschnitzelschneider bezeichnet. Es handelt sich um einen Trommel- oder Scheibenhacker, der gehacktes Holz und Büsche zu Spänen mahlen kann, die nach dem Abholzen eines Waldes übrig bleiben.
Die Komplettierung fast aller Aggregate ist identisch, sie bestehen aus einem Auffangtrichter, einem Elektromotor, Brechmesser, einem Rotor und einem Maschinenkörper.
Scheibenanlagen zeichnen sich durch ihre relativ kleinen Abmessungen und geringeren Kosten aus, während Trommelhacker eine erhöhte Produktivität aufweisen, was sie bei der Produktion großer Produktserien beliebt macht.
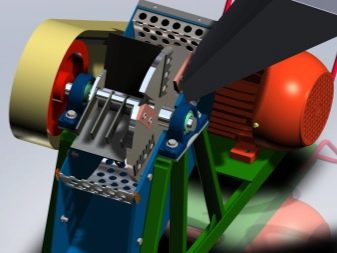
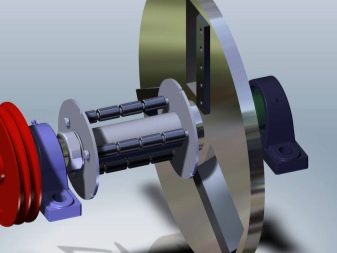
Scheibenaggregate ermöglichen die Bearbeitung von Bäumen bis zu einer Größe von drei Metern. Zu den Vorteilen dieser Art von Zuschlagstoffen zählen die geringste Menge an großen Bestandteilen am Ausgang – über 90 % der Hackschnitzel haben die erforderliche Konfiguration und Größe, große Partikel werden wiederaufbereitet. Es ist die ideale Ausrüstungswahl für die Kleinserienproduktion.

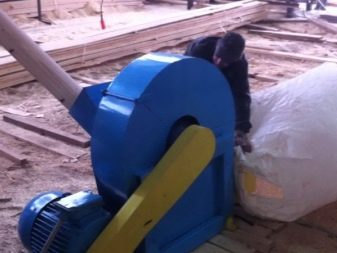
Maschine
Solche Geräte können getrost als semiprofessionell bezeichnet werden. In der Regel wird es zum Zwecke der Herstellung von Arboblöcken im privaten Bau auf Bestellung oder zum Verkauf gekauft. Es ist einfach zu bedienen, erfordert keine hohe Professionalität, die hauptsächlich mit der Einhaltung der Sicherheitsregeln verbunden ist.
Industrielle Einheiten lassen sich symbolisch in drei Schlüsselgruppen einteilen:
- manuelle Maschinen;
- Einheiten mit Vibrationspresse und Bunkerbeschickung;
- Komplexe kombinierte Einheiten, die den Empfänger mit dem Ausgangsgewicht verbinden, eine Vibrationspresse und ein statischer Former, der die Dichte der Holzbetonlösung bis zur endgültigen Aushärtung des Holzblocks zum fertigen Produkt beibehält.
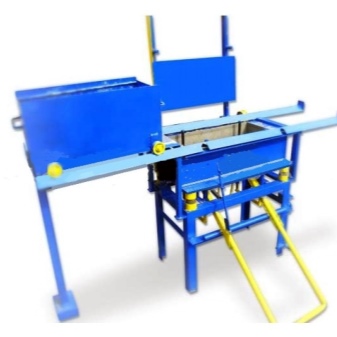
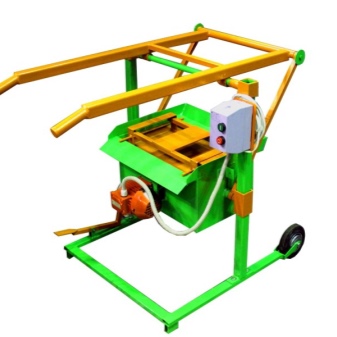
Betonmischer
Ein gewöhnlicher Mischer mit flachen Schaufeln ist nicht zum Mischen von Holzbetonmörtel geeignet. Alles erklärt sich dadurch, dass die Mischung halbtrocken ist, nicht kriecht, sondern in einer Rutsche ruhen kann; die Klinge fährt es einfach von einer Ecke des Tanks in eine andere, und nicht alle Chips sind mit Zementteig bedeckt.
Am Betonmischer SAB-400 in der Struktur gibt es spezielle "Pflüge" - Messer, die die Mischung schneiden, und es wird ein effektives (und vor allem schnelles) Mischen erreicht. Geschwindigkeit ist kritisch, da der Zement keine Zeit zum Abbinden haben sollte, bis er das gesamte zerkleinerte Material bedeckt hat.
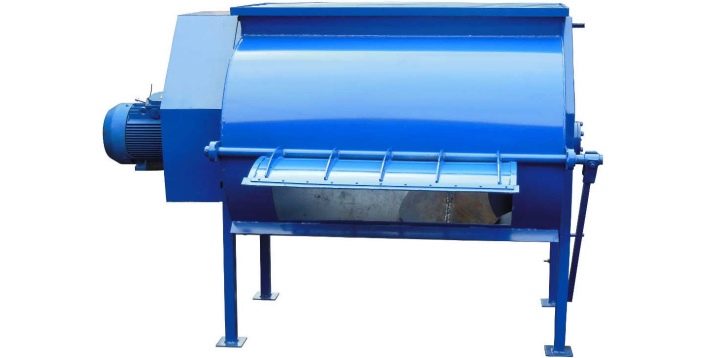
Betonmischer
Bei der Herstellung von Arboblöcken werden in der Regel von Zeit zu Zeit Impulsrührer verwendet - Baumischer. Auf großen Linien, wo die Herstellung von Baustoffen in großen Chargen erfolgt, werden Anlagen mit kontinuierlichem Charakter installiert. Um den Bedarf nicht sehr großer Industrien zu decken, In den meisten Fällen werden gewöhnliche Betonmischer verwendet, die die folgenden strukturellen Eigenschaften aufweisen:
- sind große Behälter mit seitlicher Beladung der Zutaten und Bodenentladung der zubereiteten Lösung;
- der Mischer ist mit einem Elektromotor mit Getriebe mit einer maximalen Leistung von 6 kW ausgestattet;
- Zum Mischen der Holzbetonzutaten werden spezielle Klingen verwendet.
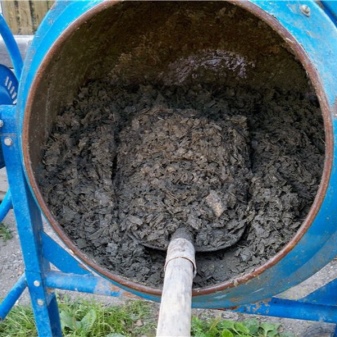
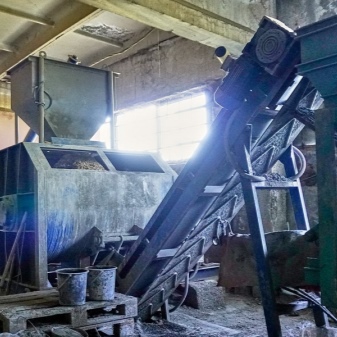
Das Volumen des Mischers wird basierend auf dem täglichen Materialbedarf berechnet, um einen effektiven technologischen Prozess zu etablieren.
Vibropresse
Die Fläche des Rütteltisches (Vibropress) hängt auch von der Größe des Formgebungsbatches ab. Die Vibrokompressionsmaschine ist ein Metalltisch proportional zur Größe des Spenders, der mit Federn ausgestattet ist und mit dem Bett (schwerer Haupttisch) verbunden ist. Auf dem Bett ist ein Drehstrom-Elektromotor bis 1,5 kW installiert, auf dessen Achse sich ein Exzenter befindet (eine Last, deren Schwerpunkt verschoben ist). Wenn dieser verbunden ist, finden regelmäßige Vibrationsvorgänge des oberen Teils des Tisches statt. Diese Maßnahmen sind für eine optimale Schrumpfung in Form der Zusammensetzung von Holzbetonblöcken und die Beseitigung von mechanischen und äußeren Defekten der Blöcke nach dem Entfernen der Form erforderlich.
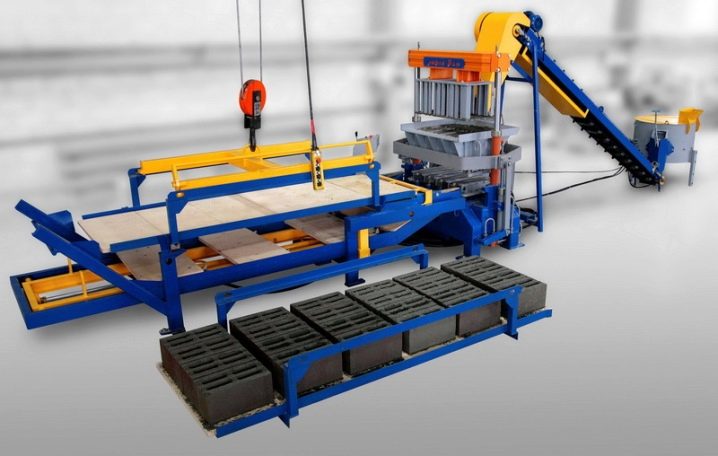
Formen
Die Matrix (Form, Pressbleche) zur Herstellung von Blöcken soll dem Produkt spezifische Abmessungen und Konfigurationen geben. Insbesondere hängt es davon ab, wie genau die Form des Blocks sein wird.
Die Matrix ist eine rechteckige Form mit einer leeren Kontur im Inneren, in die die Lösung eingefüllt wird. Diese Form bietet einen abnehmbaren Deckel und Boden. Das Formular hat spezielle Griffe an den Rändern. Im Inneren ist es mit einer speziellen Beschichtung ausgestattet, die das Entfernen des geformten Blocks erleichtert.
Grundsätzlich wird für die Innenbeschichtung ein glattes künstliches Material praktiziert, das können Plastikfolie, Linoleum oder ähnliche Materialien sein.
Trockenkammern
Fertig gepresste Arboblöcke werden zusammen mit den Matrizen in einen spezialisierten Raum geschickt.Darin wird die Luftfeuchtigkeit streng kontrolliert, wodurch optimale Bedingungen für die Trocknung des Materials geschaffen werden können.
Blöcke werden unbedingt auf Paletten ausgelegt und von Matrizen befreit. Das optimiert den Zugang von Luftmassen zum Material, dies wirkt sich positiv auf seine Eigenschaften aus.
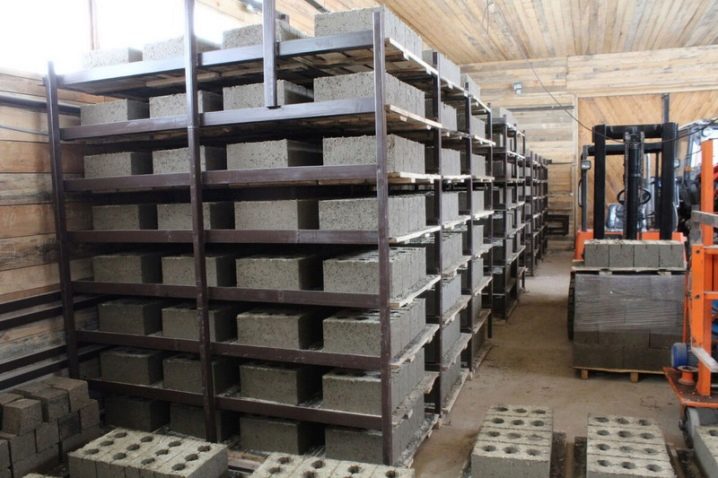
Die Anhaftung der Lösung erfolgt in der Regel nach zwei Tagen. Die Bemessungskapazität des Baustoffs wird erst nach 18-28 Tagen erreicht... Während dieser Zeit muss sich Holzbeton in einer Umgebung mit der erforderlichen Feuchtigkeit und stabilen Temperatur befinden.
Bei der Heimproduktion wird in der Regel eine gepresste Charge von Arboblöcken an einem abgedunkelten Ort ausgelegt, mit einer Polyethylenfolie und einer schützenden Stoffmarkise abgedeckt. Nach 2-3 Tagen werden die Blöcke in den Raum gebracht und in einer Schicht auf dem Steinboden ausgelegt. Nach 7 Tagen können die Blöcke in Packungen verpackt werden.
Wie wählt man Ausrüstung aus?
Um Holzblöcke herzustellen, benötigen Sie 3 Maschinentypen: für die Herstellung von Hackschnitzeln, für die Herstellung von Mörtel und für das Pressen. Sie sind sowohl russisch als auch im Ausland hergestellt. Unter anderem schaffen es einzelne Handwerker, Geräte mit eigenen Händen zusammenzubauen (in der Regel bauen sie Vibropressen selbst zusammen).
Brecher
Shredder sind mobil und stationär, Scheibe und Trommel. Disk unterscheiden sich im Funktionsprinzip.
Es ist großartig, wenn die Anlage mit einer mechanischen Rohstoffzuführung ausgestattet ist - dies wird die Arbeit erheblich vereinfachen.
Betonmischer
Ein handelsüblicher Rührer ist hierfür ideal. Für industrielle Kapazitäten, auch innerhalb der Grenzen einer Miniplant, wird ein Tankvolumen von 150 Litern oder mehr benötigt.
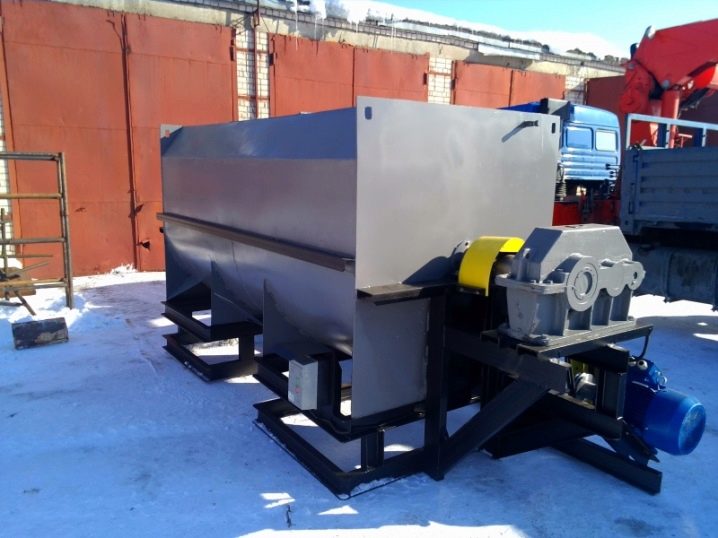
Trockenkammer
Sie können den Trocknungsprozess beschleunigen, indem Sie eine spezielle Trocknungskamera (hauptsächlich Infrarot) kaufen. Beim Kauf solcher Geräte müssen die Parameter Strom- und Energieverbrauch sowie die Möglichkeit, das Temperaturniveau und die Trocknungsgeschwindigkeit einzustellen, beachtet werden. In der Trockenkammer trocknen die Blöcke aus und sind innerhalb von 12 Stunden einsatzbereit - fast 30-mal schnellerals ohne Sonderausstattung.
Für die industrielle Produktion gilt eine hohe Geschwindigkeit als ein ziemlich wichtiger Indikator, der sich direkt auf das Einkommen auswirkt.
Wie macht man eine Maschine mit eigenen Händen?
Um eine selbstgebaute Vibrationsmaschine zusammenzubauen, werden Zeichnungen und diese Materialien benötigt (alle Maße sind ungefähre Angaben):
- Vibrationsmotor;
- Schweißer;
- Federn - 4 Stk.;
- Stahlblech 0,3x75x120 cm;
- Profilrohr 0,2x2x4 cm - 6 m (für Beine), 2,4 m (auf der Basis unter der Abdeckung);
- Eisenecke 0,2x4 cm - 4 m;
- schrauben (zur Befestigung des Motors);
- Spezialfarbe (zum Schutz des Geräts vor Rost);
- Stahlringe - 4 Stk. (Der Durchmesser sollte dem Durchmesser der Federn entsprechen oder etwas größer sein).
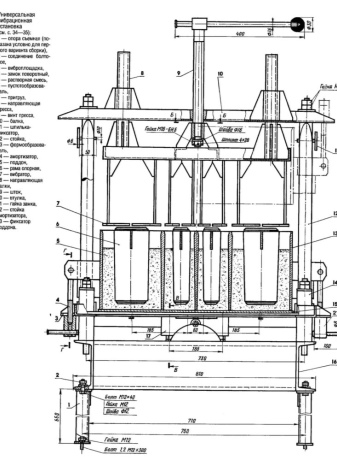
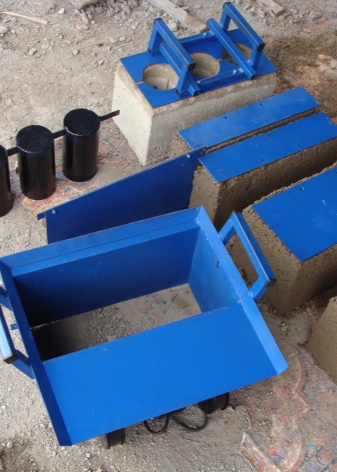
Der Montagevorgang für den Rütteltisch ist recht einfach.
- Wir schneiden das Material in die benötigten Elemente.
- Wir teilen das Rohr unter den Beinen in 4 identische Teile von jeweils 75 cm.
- Das Rohr für den Rahmen teilen wir wie folgt auf: 2 Teile je 60 cm und 4 Teile je 30 cm.
- Teilen Sie die Ecke in 4 Elemente, die Länge sollte mit der Länge der Seiten des Eisenblechs unter der Arbeitsplatte übereinstimmen.
- Schweißarbeiten: Zusammenbau des Skeletts zur Befestigung des Motors an der Abdeckung. Wir schweißen ein Viereck aus zwei 30- und zwei 60-Zentimeter-Stücken. In der Mitte werden 2 weitere kurze Elemente in einem bestimmten Abstand dazwischen verschweißt. Dieser Abstand sollte dem Abstand zwischen den Motorbefestigungspunkten entsprechen. In den Mittelteilen sind an bestimmten Stellen Löcher zur Befestigung gebohrt.
- An den Ecken des Eisenblechs schweißen wir Ringe, in die die Federn eingefädelt werden.
- Jetzt verschweißen wir das Stützbein mit den Beinen. Dazu nehmen wir Eckstücke und Rohre. Platzieren Sie die Ecken so, dass ihre Kanten von der Innenseite der Struktur nach oben und außen gerichtet sind.
- Der geschweißte Rahmen für den Motor wird mit selbstschneidenden Schrauben befestigt oder auf die Tischplatte gegart.
- Wir platzieren die Federn auf dem Stützgestell in den Ecken.Wir legen die Tischplatte auf das Gestell, damit die Federn in die Zellen passen. Wir befestigen den Motor unten. Die Federn müssen nicht befestigt werden, da die Masse des Deckels mit dem Motor sie sicher an der richtigen Stelle hält.
Das fertige Gerät kann lackiert werden.
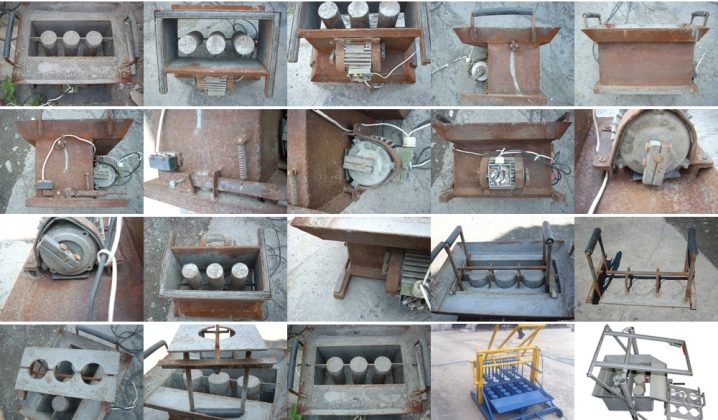
Eine Übersicht über Anlagen zur Herstellung von Holzbetonsteinen finden Sie im nächsten Video.
Der Kommentar wurde erfolgreich gesendet.